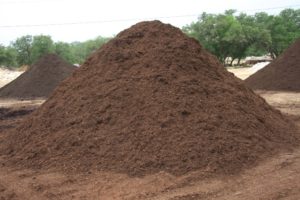
Did you know there is a requirement for how many inches of mulch you must have on a playground at any given time? It’s a safety measure for public spaces such as schools and parks and recs. Mulch is normally delivered commercially by the cubic yard and not by the bag, so envision the truck dumping the mulch in a designated place so the maintenance guys can get to it. Now that you have the mountain of mulch firmly pictured in your mind, ask yourself, how are you going to prevent your mulch from walking away overnight? How do you measure how much is needed for a job? That mountain of mulch represents a portion of your budget and is supposed to cover a specific amount of space to ensure the depth needed to pass inspection (or avoid a lawsuit).
The big question now is, do you track your mulch as inventory to be used in your work orders? You should be, unless your budget is so big that you don’t care if one or ten of your maintenance guys mulches his flower beds with your mulch. Wouldn’t it be nice to have a budget like that? We’re betting you’re in the same shape as a lot of our clients and are on the ‘do more with less’ budget plan, though. So again, do you track your mulch as inventory?
We find this question gets at the fundamental issue of most CMMS programs.
We provide all the modules available in our software to our clients, while others charge for each individual module. So if you’re using a product that charges for each individual module and you haven’t found the time, money or the motivation to purchase the inventory module because your spreadsheet has worked for years, thank you very much, it might be time to chat with us to see what you can get and whether it fits in your budget. We can’t say it too many times – maintenance resource planning is about looking at maintenance as a whole and not trying to cobble together pieces and parts to figure out where your money, time and resources are actually going. Then integrating your data with other departments, like finance.
In practice, utilizing your integrated inventory module with your work orders looks something like this.
Your maintenance guy goes out and measures the mulch level and finds it to be low, so he enters a work order that includes how much mulch he thinks will correct the issue in the inventory section of the work order form. The work order is approved and the maintenance person it was assigned to mulches the playground using the amount of mulch indicated. Hopefully, someone re-measures the mulch level. When the work order is complete, the total mulch used is entered in the work order and removed from inventory when the work order is closed. In a perfect world, that information is transmitted by the CMMS over to finance so they can track spending. All of this information is provided in one work order, which you would have had to do anyway, right?
The bottom line, tracking mulch seems silly but it’s part of your inventory and you spent money on it. You should know where the money went and when it was spent so you can more accurately budget for the following year. Integrating your data, which we do for our clients, is just the icing on the cake. We find integration makes it easier than maintenance continuously running reports for finance, which reduces the workload for everyone.