We have traveled all over the country working with maintenance departments of different sizes, complexities and responsibilities. We’ve seen great maintenance shops and “not so great” maintenance shops. I’ve noticed a striking relationship between the use of technology and the overall well-being and professionalism of an organization. In short, great maintenance shops take advantage of technology.
Let us set the scene. We walk into a maintenance shop and see a group of tradesmen that are appropriately dressed, well equipped to do their job and have generally good attitudes. This scene is always coupled with a clean shop, a comprehensive PM program and great use of technology. Not just a presence of technology, but a use of technology. The relationship is proportional. The more that technology is utilized the better the shop.
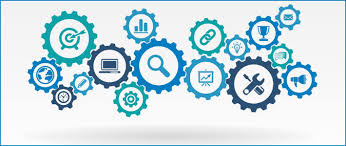
Just spending money to purchase technology does not make it successful. After the purchase, policies and processes must be put in place to take advantage of the purchased system, including building KPI goals and measurements. If this is done properly the technology will pay for itself in savings of money and manpower. Use these savings to implement new technology and the processes to go with it. In turn, you will get more savings. This cycle will repeat over and over again.
For example…
A computerized maintenance management system (CMMS) is purchased. Procedures and policies are put in place to take advantage of the work order management benefits of the system. A 10% savings is discovered in labor and expenses. That equals 1 man year saved per 10 tradesmen and $10,000 for every $100,000 in expenses. The savings are used to implement a PM and asset program in the CMMS. Another 10% increase in savings is discovered. The PM system is expanded. Another 10% savings. The warehouse portion of the CMMS system is put into action. More savings are discovered. The money saved by properly tracking the inventory allows the purchase of a mobile work order system. Before you know it, 95% of your maintenance is planned work, the tradesmen take great pride in keeping their systems and work ahead of schedule, management can justify every FTE/PTE and expense and maintenance is seen as an asset and leader in the enterprise rather than just a necessary expense or cost center.
To be clear, maintenance will always have a cost, but those costs don’t have to come without methods and technology to reduce those costs. Simple technology started it all and grew into a complex system of interwoven platforms and systems that exchange data, work together and help maintenance avoid obstacles and pitfalls. The resulting data allows budgets to be created easily and accurately, expansion to be justified and capital expenditures to be seen and planned for long before they are needed.