Your next step is preventive maintenance (PM). We’ve put our work order process in place and have collected our asset information. Most CMMS systems handle this task in different ways but the basic principle is the same. You will want to create two types of PMs, routine maintenance and preventive maintenance.
Why Have Two Preventive Maintenance Types?
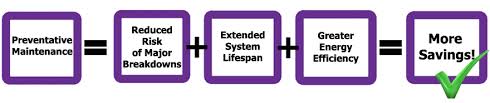
Routine maintenance refers to tasks that happen on a normal routine that are not completed on a specific piece of equipment. Examples of routine maintenance are Indoor Air Quality (IAQ) tests, safety inspections, grass cutting, filter changes, etc. These are all important tasks but are not completed on a specific piece of equipment. Please don’t underestimate the importance of tracking inspections in your CMMS system. Inspections are usually completed to reduce liability. For example, IAQ tests may be done annually. The reason is to ensure safe locations for employees, students and/or staff. The IAQ testing alone is not enough. In the event of a lawsuit you will need to have documentation of due diligence. Adding the IAQ test as an annual inspection in your PM system will ensure you are meeting compliance and that the work and results are documented.
The second type of PM is asset specific. Examples are boiler, vehicle and roof PMs. Each of these items should be entered in your CMMS as an asset and you will need to schedule your PMs for each frequency. These PMs keep your valuable building and mechanical assets in good condition. It has been proven over and over again that a good PM system can save 30% of your annual budget in saved materials and manpower. What is not so obvious is the improved moral that comes along with a day well planned instead of a day spent reacting to emergencies. Add the benefits of having the data at your fingertips to measure your KPI’s and make informed decisions about your facility master plan, and the necessity of having a implementing your PM schedule is hopefully very obvious.