The following is a ‘guest’ post written by TeamWORKS CEO, Craig Drouillard. Happy reading!
For the past 15 years I have been part of computerized maintenance management system (CMMS) software and service companies. The last 9 years have been with TeamWORKS, a company I started to fill the vacuum of inexpensive, world class CMMS. During this time I was involved with every aspect of a CMMS company – building software, managing projects, installation and training and the other duties surrounding software.
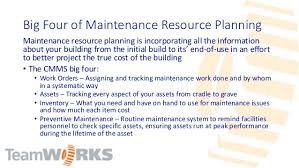
About 10 years ago, (I was working with my previous employer), there was a shift in needs. Open technology started to creep into the marketplace. Databases could talk to each other more easily and networks reached deep into the infrastructure of practically every enterprise in need of a CMMS. As a result our clients saw some advantages of the access offered through networking and open protocols. There was a need for integration. It makes sense, why enter data twice if an application or database routine can do the work for you. As I started TeamWORKS I focused on the CMMS needs of our clients. I am a firm believer in “you can’t be all things to all people” so I narrowed the beam and kept my focus. In the meantime I missed opportunities to integrate, consult and prepare maintenance management organizations for areas beyond TeamWORKS CMMS.
Then the U.S. economy hit the brakes and nobody had enough money. Maintenance departments are being forced to do more for less, front offices are looking for areas to reduce cost and employees are being cut. At the same time maintenance needs are rising as equipment is extended beyond its typical lifecycle.
As a result, budget managers are utilizing the Enterprise Resource Planning (ERP) software to look for areas to cut back. Maintenance and Operations do not typically care for ERP software. ERP software builds budget projections by looking at the past. That is great for budgeting but does not help the maintenance manager. Budgeting is a small part of the job. Controlling the budget requires work planning, preventive maintenance, asset lifecycle forecasting and many other forward looking processes. The requests for integrations have grown to incredible numbers as maintenance looks for a way to satisfy the business needs of the enterprise while continuing to have a forward looking CMMS.
As we got more of these requests, TeamWORKS decided to embrace the need. It simply makes sense to shift the focus from CMMS provider to MRP provider. We are the best available to do this work and I have always seen the value.
Working with an MRP company rather than a CMMS company has huge benefits. CMMS is designed to manage work flow, preventive maintenance and the typical aspects of maintenance and operations. You buy the software, buy the service and, for the most part, you’re done. An MRP company takes a broader and deeper look at your resources and infrastructures. The goals are simple. Increase efficiency and accountability, reduce costs through the use of technology and increase the knowledge base for making future decision.
Before you know, you have saved a huge percentage of your budget, your operations are running smoother and you’re the hero!
The bottom line is that MRP is a new way of looking at old problems. ERP versus CMMS, budget versus manpower, preventive maintenance versus corrective maintenance are some of the many areas that are cleared up as you move toward viewing your maintenance and operations through the eyes of a MRP professional.